Radiography Testing Services
STUDENT RESULTS RVSGLOBE
Click HereRVSGLOBE RADIOGRAPHY TESTING SERVICES
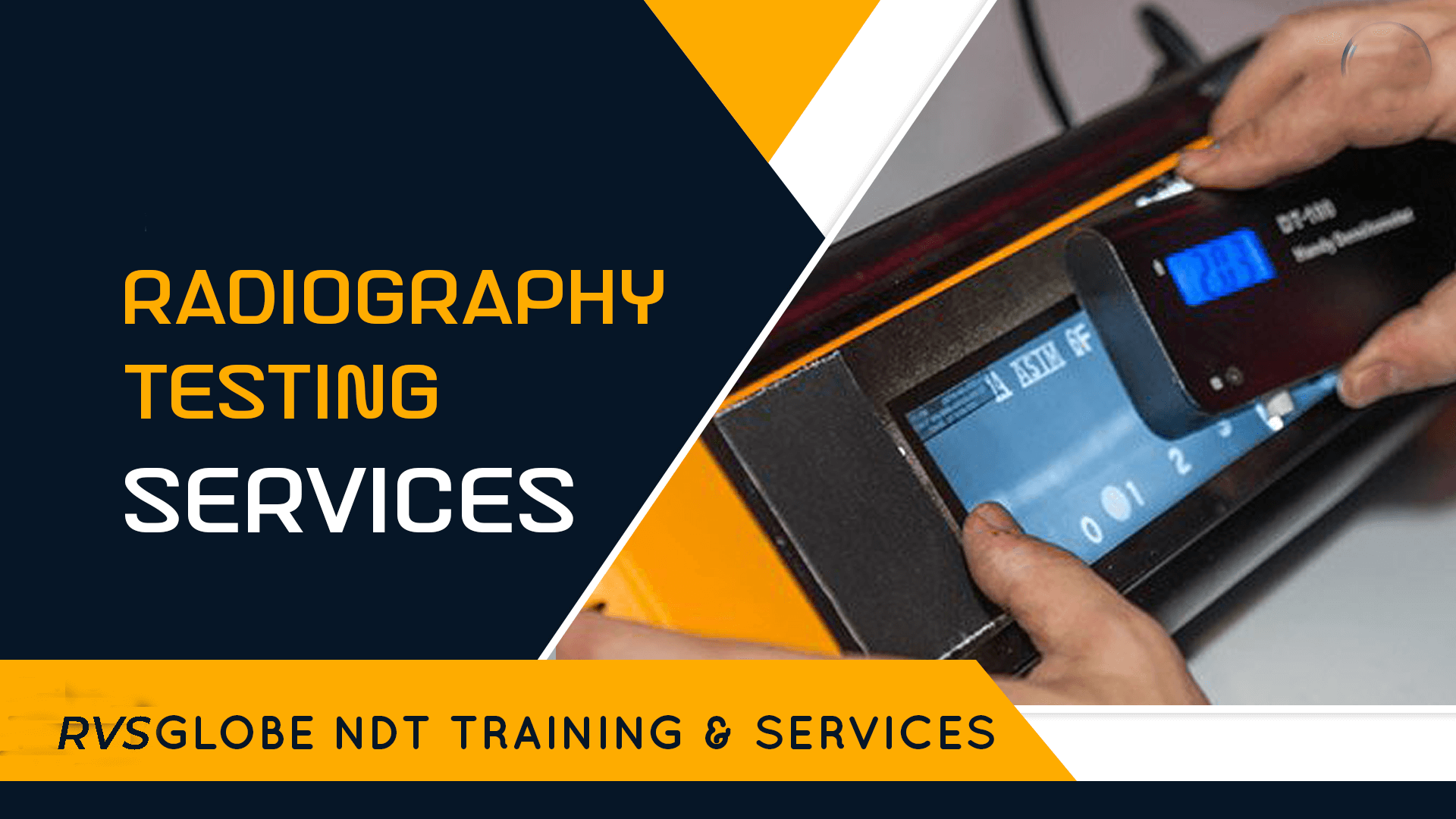
RVSGLOBE RADIOGRAPHY TESTING SERVICES IN HYDERABAD
RVSGlobe NDT services in Hyderabad, India present the best Radiography testing services in Hyderabad. Our radiography testing services include various Gamma Ray Radiography Inspection using Iridium 192 sources and other testing methods include the X-ray Radiography testing, Magnetic Particle Testing, Ultrasonic Testing, Penetrant testing and Eddy Current Inspection Methods.
RVSGlobe services in Hyderabad is considered as the India’s fastest growing NDT services globally. It is fully equipped with wide range of equipment’s based on modern technology and industrial standards meeting the international standards.
RVSGlobe is fully loaded with professional, experienced engineers to take care of radiography testing services in Hyderabad. Our industrial radiography testing services are used among variety of applications. It is most widely observed in performing two-different sources of radiations like both X-ray and Gamma ray sources.
The choice of radiation sources along with their strengths can be depend on multiple factors like component size and material thickness. The broad group of both Gamma ray and X ray sources contain various camera choices according to radiation strengths and requirements.
The Gamma ray or Radiography and X-ray labs are approved by “Center for Military Airworthiness (CEMILAC).” It is a Defense organization under the Ministry of Defense, Government of India for Non-Destructive Testing (NDT) of aerospace components or Airborne Systems for Indian Military Applications.
X-Ray capabilities of CR Services are run by the gamut from 4 MEV units. These are utilized to radiograph the extreme large and thick forgings and castings and the portable cameras are used to field wield applications and to inspect the thin raw materials.
Generally, Gamma sources are varied from a very low level fluoroscopic units to perform the real-time corrosion under surveys of insulation’s. It includes Iridium (Ir192) and Selenium (Se 75) sources used for various weld inspections, to Cobalt (Co 60) inspections for thick component testing and likewise.
RADIOGRAPHY TESTING ADVANTAGEOUS
RADIOGRAPHY TESTING DISADVANTAGEOUS
Radiography testing services are widely used extensively on weldments and castings. This radiography testing method is well suitable for testing multiple semiconductor devices for broken wires, cracks, foreign material, unsoldered connections, and misplaced components.
Radiography sensitivity generally depends on variety of factors like type of flaw, type of material, and product form. Radiography can be performed to both ferrous alloys, as can non-metallic materials and composites.